受注につながる技術提案,施工条件やコスト条件などの課題解決,将来の市場優位性の確立——。これまで培った技術・ノウハウに,新たな発想をプラスして, 課されたハードルをクリアする。新たな技術がどう生み出されたのかを追う。
自動車のタイヤ交換などで使うジャッキ。大型のジャッキは,建設現場でリフトアップやスライドといった構造物や建物を“動かす技術”に使われる。そこには機電の技術力が発揮される。
当社の旧本社ビルの解体で実用化した高層ビルを下層階から解体する「鹿島カットアンドダウン工法」,東京国際空港国際線地区旅客ターミナルビル等新築工事(A・B工区)における大屋根スライド工法などは,ジャッキの制御技術や計測技術がキーテクノロジーとなった。全長178m,幅95m,総重量5,000tの大屋根を動かす工法が,どう開発されたかを紹介する。
大屋根のスライドを支える
新たな国際線ターミナルビルの大屋根工事は当初,構造体を吊り上げる「リフトアップ工法」が検討されていたが,直下に京浜急行の軌道があるため,大型クレーンを設置することができなかった。そこで大屋根を滑らせながら順次組み立てる「スライド工法」を導入。現場とともに部署横断組織で工法に必要な技術開発を行った。
機械部技術4グループ(建築)の水谷亮次長は,京浜急行の上大岡駅で採用した「スーパースライディング工法」が使えると直感したという。約15年前に行われた国内最大規模のスライド工法で,駅ビルとなる躯体を軌道の直上でスライドさせた。また,橋梁の横引きなどの実績からも多くの工夫や留意点の情報を収集することができた。今回の大屋根は,柱脚を切り離すと不安定な構造のトラス架構。どうスライドさせるかが技術的に大きな課題だった。そこで,風や構造設計の専門家とタッグを組み,風対策やスライド中の構造安定性などを検討し,スライディング機構,手順,制御,計測などのジャッキシステムを計画していった。
建築工事で使う技術に対して,土木・建築に拘らず様々な情報をすぐに取り出し活用できるのも,機電部門ならではの持ち味だという。
大屋根とレールの間に挟み滑りやすくするジャッキ
大屋根を押し出しスライドさせるジャッキ
これまで多くの建設機械や工法を開発してきた水谷次長
大屋根工事は,航空機運行の妨げとならないように,クレーン作業全般において高さ制限が設けられていた。「クレーンの先端にGPSアンテナを取り付け,現場事務所のPCサーバーで高さ監視ができないか」と発想したのは本工事を担当した石田武志機電課長(現東京建築支店東京駅八重洲中央棟新築工事事務所)。高さ情報のほかに,早期地震警報システムからの地震情報,雷・強風情報も同時に配信できる仕組みとした。現場内にメッシュネットワークを構築し,現場の何処にいてもPDAなどで確認可能。通常はオペレータからの無線連絡となるが,何処でも誰でも監視ができる仕組みになり,現場では高い評価を得たという。
現場での“ひと工夫”も技術開発のうちである。
GPSアンテナを設置したクローラークレーン
様々な機電技術を現場に
適用する石田機電課長
地下トンネルを構築するシールド機は,都市の過密化に伴い,社会インフラを地下に整備する必要性から,ここ数年,活発な技術開発が行われている。キーワードは,大断面,大深度,長距離,高速施工,断面の最適化。進化を続けるシールド技術の裏に機電の力がある。
世界最長・最速記録を残す
東京土木支店中央環状品川線統合事務所の米沢実副所長は,入社以来,シールドや山岳トンネルの現場を経験し,現場サイドから技術開発を進めてきた。「こんなことができたら良いなと思うことには,全て挑戦してきた」と力を込める。5年前,東京電力の東西連係ガス導管工事の副所長を務め,世界最長・最速の記録を残す。引渡しまで37ヵ月という短工期で,約9kmの長距離トンネルを構築することが条件だった。
そのため,シールド機について,様々な角度から耐久性・信頼性を検討。セグメント搬送設備について,坑内のストックシステムやバッテリーロコの自動運転,台車への積載方法などを考案し,長距離・高速施工を目指して,あらゆる技術を提案した。結果,1台のマシンで9.03kmを無事に掘進。これまで300〜400mだった月進量に対し,665m/月を達成した。瞬間時には1,168m/月を記録。これは密閉型シールドでは世界最速だ。
土木管理本部の吉川正土木技術部長は「土木と機電の両方が出来る人。先進的な機械の開発だけでなく,現場目線で目立たないところに工夫を凝らし,工期短縮,利益向上に結びつけるプロ」と評する。本人も専門を意識して仕事はしていないと話すが「最小限の設備で最大の結果を残す」。この言葉に機電社員としてのプライドを感じさせる。そして今,首都高速中央環状品川線の現場で,大断面・長距離・高速施工に挑戦を続けている。
大断面・長距離・高速施工に挑戦を続けている米沢副所長
円形から矩形,そして自由断面へ
「円形でないシールドは将来必ずニーズがある」。機械部の永森邦博担当部長が,断面の最適化に挑んだのは約12年前のこと。シールドトンネルは土圧・水圧に強い円形が一般的だが,鉄道や道路といった断面が大きい交通インフラでは,トンネル上下の余分な部分を掘削してしまうため,残土が多くなり環境負荷につながるからだ。
「これまで蓄積されたデータが重要なんですよ」と永森部長が言うように,機電部門の技術・ノウハウを活かし「WAC工法」→「EX-MAC工法」→「アポロカッター工法」へと進化させてきた。開発毎に技術・ノウハウが再び蓄積され,新たな開発へのステップとなっている。
「アポロカッター工法の開発」が平成22年度(社)日本建設機械化協会(JCMA)貢献賞を受賞した。受賞者を代表して表彰状を受け取る永森担当部長
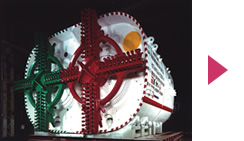
WAC(Wagging Cutter Shield)
工法
1999年に,きらめき通り地下通路(福岡市)で初めて実用化した矩形シールド工法。伸縮自在なカッターをワイパーのように揺動させ,矩形トンネルを構築する。円形シールドのデータをもとにカッターの揺動力や伸縮力,潤滑油の量などを決定しマシンを設計。この第1号機のデータが,京都市営地下鉄の六地蔵北工区(写真)の工事に活かされた。
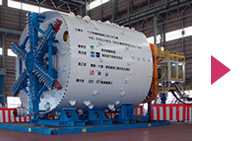
EX-MAC(Excavation Method of Adjustable Cutter)工法
WAC工法の基礎技術を応用し,カッターの伸縮幅をより長くすることにより,一つの回転軸で矩形に近い複合円形断面を実現。土圧変動抑制装置を考案し,安定した掘進を可能にした。2005年に,東京メトロ副都心線の神宮前工区に適用され無事に掘進を終えた。
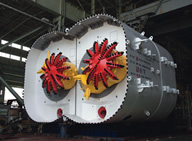
アポロカッター工法
究極の断面最適化といえる自由断面を実現した工法。硬質地盤に対応するため,公転ドラム,揺動フレーム,そして高速回転カッターヘッドからなる機構を考案した。複雑な動きをする全く新しいマシン。切削性能,攪拌性能などの実証実験を繰り返し,マシン設計にフィードバックした。東横線が運行する直下での掘進という難工事を無事に完了させた。実証実験のデータを設計に反映させた成果である。