A4CSEL®のコンセプトは多くの重機を一人で操って生産性を上げること。
最初のターゲットは重機土工の自動化だ。日々変わる土木現場の環境に応じて変えていかなければならない作業を自動化するための絶え間ない進化と深化の様子を紹介する。
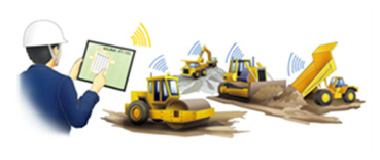
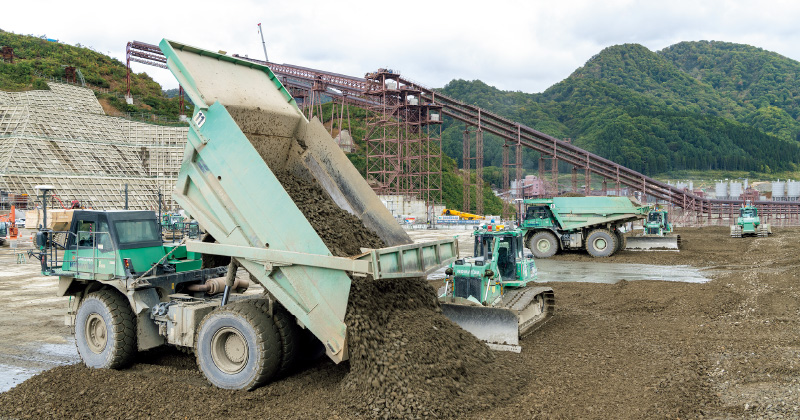
ダンプトラックから堤体上に荷下ろしされるCSGを待ち構える自動ブルドーザ
photo: takuya omura
成瀬ダム堤体打設工事(第I期)
- 発注者:
- 国土交通省 東北地方整備局
- 場所:
- 秋田県雄勝郡東成瀬村
- 設計:
- 日本工営
- 規模:
- 台形CSGダム 堤高114.5m
堤頂長755.0m 堤体積485万m3 - 工期:
- 2018年5月~2023年3月
(東北支店JV施工)
秋田と岩手,宮城の3県にまたがる栗駒山の北側に位置する秋田県雄勝郡東成瀬村。ここに,当社が世界に先駆けて開発した建設機械の自動運転を核とした次世代建設生産システム「A4CSEL」により堤体打設を行う成瀬ダムの現場がある。何台もの重機が人手を介さず,自動運転でダム堤体を積み上げていく。いわば,ダムをつくる3Dプリンターだ。
当社は,振動ローラを皮切りにブルドーザ,ダンプトラックを自動化して2015年から3つのダム工事に適用してきた。4つめの現場となる成瀬ダム堤体打設工事では20数台の自動化重機が連携して,ダム堤体工事の主要作業である「材料運搬」,「まき出し」,「締固め」を昼夜にわたり数十時間連続で自動施工している。まさに,A4CSELの集大成の姿がここにある。
成瀬ダムは,堤高114.5m,堤頂長755.0m,堤体積は485万m3の台形CSGダム。現地発生材(石や砂礫)にセメント・水を混合してつくるCSGを堤体の材料とする台形型のダムである。台形形状は安定したその形状から必要強度を小さくでき,かつ現地発生材を使用するため,環境負荷低減やコスト縮減が期待できる。日本屈指の豪雪地帯で冬季は堤体施工を休止せざるを得ない地域で日本最大級のCSGダムを建設するため,1ヵ月当たり25万~ 30万m3というこれまでの同種工事の2倍以上の大容量高速施工が要求されている。
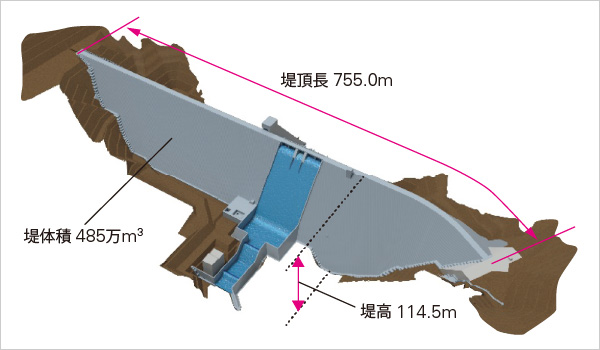
完成予想パース
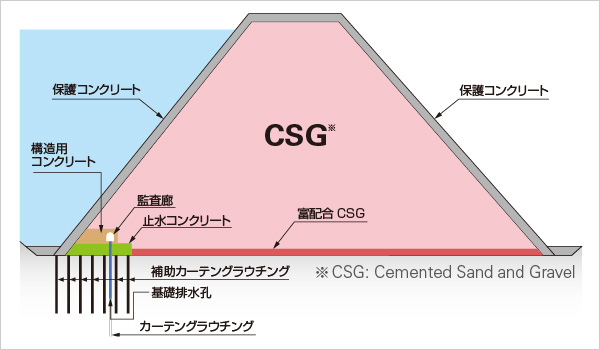
台形CSGダムの断面イメージ
「前代未聞の高速施工です。同時に,品質も確保しなければなりません。プログラム通り作業手順を忠実に守るA4CSELは,この工事に欠かせない存在です。そして何より,A4CSELで施工中のエリアは人が全く立ち入らないので,安全です」。このように話すのは,当社JVの奈須野恭伸所長だ。宮ケ瀬ダムを皮切りにこれまで主にダム現場を担当し,前任地である大分県の大分川ダムで2017年にブルドーザとダンプトラック,振動ローラの3種類の自動化重機による導入試験を目の当たりにして以来,A4CSELを自身の現場で実現させたいという強い思いを持っていた。
従来の有人施工ではオペレータの熟練度に関係なく,どうしても作業にムラができてしまう。それに対して,A4CSELは最適化された施工計画とそれを確実に効率よく実施する自動運転プログラムによって,規定通り25cmの厚さにCSGをブルドーザでまき出し,それを1回の打設につき合計3層75cm分,正確に積み重ねていく。施工要領に基づいた作業通りに要求品質を確実にクリアできる上,すべての作業内容のトレーサビリティも確保できる。
奈須野恭伸所長
photo: takuya omura
しかも,A4CSELは燃料補給のときを除き,連続して施工することが可能だ。オペレータで同じことをしようとすると,途中で交代したとしても,その激務に耐えられないだろう。
奈須野所長は,「自動化は『人減らし』と受け取られがちですが,労働人口の減少や熟練技術者の高齢化など担い手不足となっている現実を,我々建設会社が一番深刻に受け止めています。30年前,宮ケ瀬ダムの建設に携わっていた時は想像もしませんでしたが,自動化を進めていかないと,これからの社会に対応できなくなるときが必ず来ます」と,将来への危機感とA4CSELの必要性を力説する。
現場では,ブルドーザと振動ローラが自動で稼働している。現段階では他の工事車両と共有の工事用道路を走行するため,ダンプトラックはオペレータが運転しているものの,すべての作業が堤体上で行える体制になる2023年度には,清掃車などを含む5種類合計23台の自動化重機が堤体上で稼働する計画だ。
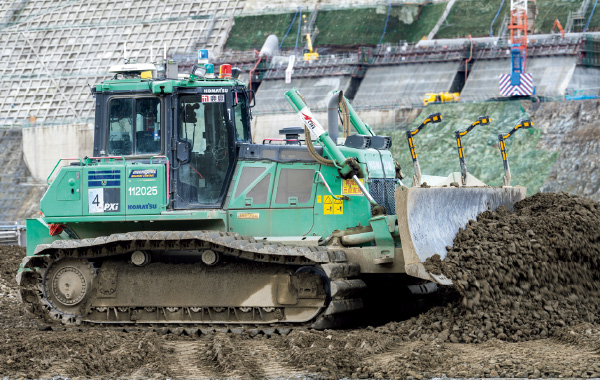
CSGを敷き均す自動ブルドーザ
photo: takuya omura
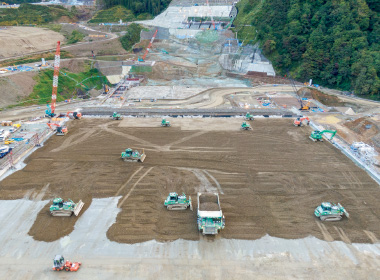
A4CSELが活躍する
堤体上の施工エリア
photo: takuya omura
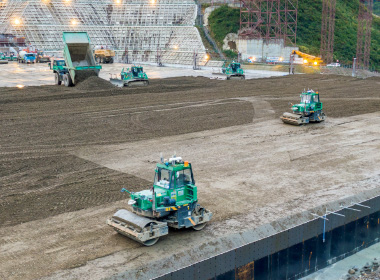
敷き均されたCSGを
自動振動ローラが転圧する
photo: takuya omura
目標達成に向かって繰り返す進化と深化
成瀬ダムが位置する秋田県東成瀬村は国内有数の豪雪地帯である。このため,堤体の工事は11月中旬までで,それ以降,雪が解ける4月上旬まで休工となる。
総勢15名のA4CSEL担当メンバーとともに現場に常駐する当社JVの出石陽一副所長は次のように説明する。「4月~11月は,日々の自動化施工で生じる問題や生産性をより向上させるための課題を施工を進めながら解決していって,システムの信頼度や成熟度を上げる『深化』を繰り返しています。外見は同じように見えますが,中身は日々変化しているのです」。
一方で,冬季の施工休止期間はA4CSELにとって「進化」を加速する重要な日々となっている。施工中に生じた問題や,次年度に必要な新しい施工方法の検討,自動機械や自動運転の性能・機能の向上などの課題を持って帰ってきた現場メンバーと,R&Dの中核としてAI手法の導入,自動化機種の増強,他工種への利活用などの検討を進めている本社や技術研究所のメンバーが一緒にA4CSELを変えていっているのである。
堤体打設1年目の2020年は,1時間当たりの打設量230m3から自動化施工をスタート。段階的に打設スピードを上げ,2年目の昨年4月には,1時間当たり750m3を達成した。打設3年目となる今年はプラントをさらに改良した上で,前人未到の1時間当たり900m3の連続打設を目指すという。これまでに蓄積した施工データの分析からムダを削ぎ落とすとともに,一つひとつの動作速度を上げるなど,作業手順や方法にも直接手を加えることで一層のサイクルタイム短縮に挑戦している。
出石陽一副所長
photo: takuya omura
A4CSELは,これまでの勘や経験,職人技に依存してきた「定性的」な生産体制を,生産工学を基にした「定量的」なシステムに変える「現場の工場化」を目指している。この根幹をなすのが,品質と作業時間のバラツキがない上手な作業と,それを効率よく動かす最適な計画である。どのように運転すれば良いのか? ハンドルのさばき方やブレードを動かすタイミング,アクセルの踏み込み方に至るまで実際の熟練オペレータの操作データを取得する。一連の作業を分解することによって動作単位で標準化し,AI手法などを駆使して作業条件毎に標準動作を組み合わせることで一連の作業が定量化できる。作業のやり方から考えることで,ものづくりの基本に立ち返り,生産性の向上が図れるのだ。
成瀬ダムの右岸側サイトに設置されている管制室からA4CSELを運用しているのは「ITパイロット」。彼らの多くは土木工事の施工経験を積んできたA4CSELの開発メンバーだ。ITパイロットたちは昼夜にわたり自動化機械を管制しつつ,施工計画の立案や施工結果の分析,プログラムの改良・開発といった業務をこなす。
自動化機械の制御,施工計画の最適化,深層強化学習など,先進的かつ高度な部分は先端IT技術者によることになるが,「施工をよく理解しているITパイロットの技術をさらに向上させれば,日々刻々と変化する現場に応じたシステム改良に迅速に対応できるようになり,生産性を向上させることができる」と出石副所長は強調する。
現場での問題を迅速に解決するにはその場でプログラムを修正することが必要となる。このスキルアップのために,社外のエンジニア(先端ITベンチャーCEO)を講師として招き,「寺子屋」と呼ぶ勉強会を2019年から継続している。「自分でつくり変更したプログラムが日々の生産性を変える。その醍醐味を実感したメンバーの目の輝きに確かな手ごたえを感じています」(出石副所長)。
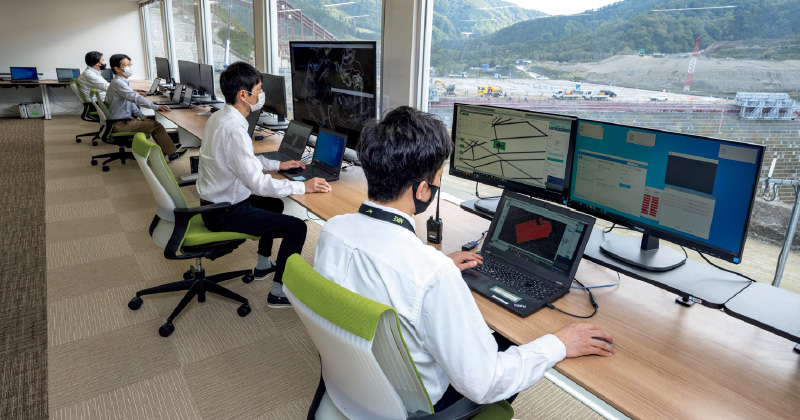
A4CSELの管制室。ITパイロットが4名1組でA4CSELを管制する
photo: takuya omura
成瀬ダムの現場に着任してからプログラムを学んだという社員も少なくない。ITパイロットの中核を担う菅井貴洋課長代理もその一人だ。A4CSELが初めて現場導入された福岡県の五ケ山ダムに勤務。現場担当者として2015年の自動振動ローラと自動ブルドーザの実証実験の動きを見て,自動化機械群の動きに無駄がなく衝撃的だったという。いつか自分も開発に携わってみたいと思ったそうだ。
菅井課長代理はITパイロットに求められる適性について,土木技術者の立場から次のように語る。「私は入社時から自らの手でコンクリートにバイブレーターをかけるなど,ものづくりに興味を持って現場を観察していたことが今の業務に活きています。もし,新入社員時代に現場経験がなかったとしても,重機の動き方一つから作業者目線で現場を見ることになるので,作業方法を考える力が自然に養われるでしょう。ものづくりをゼロから考えてみようという自発的な姿勢が常に求められています」。
菅井貴洋課長代理
photo: takuya omura
総合力を活かしA4CSELをアシスト
A4CSELは,汎用の建設機械を自動仕様に改造する技術,AIで分析した熟練者の操作データを取り入れることで,状況に応じて安定した品質で作業させる自動運転技術,そして,多数の自動化機械を連携させ,最も生産性の高い施工計画に基づいて稼働させる最適化技術で構成されている。この構成技術をブラッシュアップし続けた先にA4CSELの深化と進化がある。稼働開始してから間もなく2年が経とうとしている成瀬ダムのA4CSELも毎日のように変化している。例えば,自動ブルドーザでのまき出し作業は基本的には標準動作の組合せで成り立っている。しかし,成瀬ダムは台形であり,まき出しエリアの大きさや形は毎日変化する。また,堤体上や内部に構築する設備の影響で,複雑な形状に対応しなければならない。すなわち,実現場へ適切に対応するためには標準動作自体の見直し,組合せの変更が常に必要となる。デジタル技術を背景とした先進の施工システムであっても「経験値」を積むことで技術は深化していく。
それとともに,A4CSELの深化のためには構成技術の向上だけではなく,現場の工夫が必要だ。これまでの施工方法や作業方法をすべてそのまま自動化することは難しい。A4CSELを適用しやすい施工方法を見出すことが重要であり,作業条件を安定させることが現場の工場化を実現する鍵の一つである。ここに当社がこれまでに培ってきた総合力が余すことなく活かされている。例えば,自動ブルドーザのまき出し作業においてダンプトラックから荷下ろしされるCSGの体積と荷下ろし形状が常に一定であれば,自動ブルドーザの作業が事前に計画できる。現場の工場化の基本となる供給材料の安定化である。
ところが,実際に現場で試験してみると,一筋縄ではいかなかった。「事前に同じ条件で何度もCSGを試験練りしましたが,CSGの状態を一定にするまでだいぶ苦労しました」。このように振り返るのは,当社JVの神戸隆幸副所長だ。2010年,北海道の当別ダムで,世界初のCSGダムを施工した経験を持つ。
材料性状の安定化とともに,ダンプトラックの構造も改良した。ベッセル(荷台)の後端にテールゲートを追加。さらに,材料の出方を一定にするハの字形の金属製ガイドを設けた。ダンプアップした際,材料が勢いよく飛び出さないように上から押さえ,一点に向かって滑り落ちるようにするためだ。
神戸隆幸副所長
photo: takuya omura
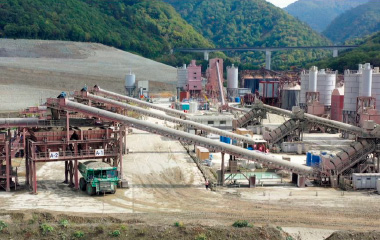
プラントを出発するダンプトラック
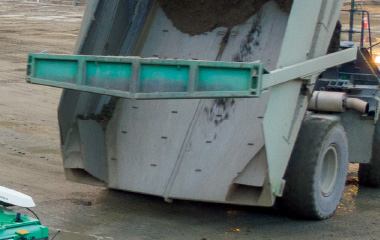
改良されたダンプトラック
photo: takuya omura
A4CSELに合わせ施工方法も最適化へ
A4CSEL の高速大容量施工を実現するためには,施工速度に合わせたCSG材料の製造システムを代表とする付随作業の高速化が不可欠。その一つに「置き型枠自動スライドシステム」がある。
堤体上では,CSGの打設と並行して,堤体の上下流面を覆う厚さ1.6mの保護コンクリートを打設する。成瀬ダムでは,H鋼を「置き型枠」として利用することから,堤体の上流面と下流面はともに1段75cmの階段状になる。置き型枠は,1本5m,高さ80cm,幅40cm。堤体を高さ75cm打設するごとに,3段下から置き型枠を引き上げて,次に打設する場所に移動する作業が繰り返される。
工事発注時の計画では,置き型枠の移動は堤体上に配置する25tクレーンの使用を想定していた。しかし,この方法では,足場の設置やクレーンの移動などに,置き型枠1本当たり50分ほどかかる。これでは,大量の作業班を投入しないと,A4CSELによる打設サイクルに間に合わない。ただでさえ,作業には,1ヵ所につき5名の人員を必要とした。また,施工する堤体が高くなるほど,施工エリアは狭くなる。クレーンを配置するスペース的な余裕がなくなるのは,目に見えていた。
当社JVが開発した置き型枠自動スライドシステムは,こうした課題を階段状になった堤体の表面に台車を配置することで一挙に解決。台車は3種類あり,このうち,「置き型枠自動スライドリフタ」が台車に取り付けた天井クレーンと,自動玉掛け装置によって,全自動で置き型枠を吊り上げる。仮設足場も堤体上のクレーンも人手も削減でき,作業時間は置き型枠1本当たり10分ほどで済む。
このほかに,打設時に型枠を押さえる「おもり台車」や,保護コンクリートに15mおきに目地を設置する際,ロール状に巻かれた塩化ビニル製の止水板を吊り上げる「止水板台車」を開発。ともに堤体上にクレーンを配置する必要がなくなり,作業時間・作業人員とも大幅に削減した。
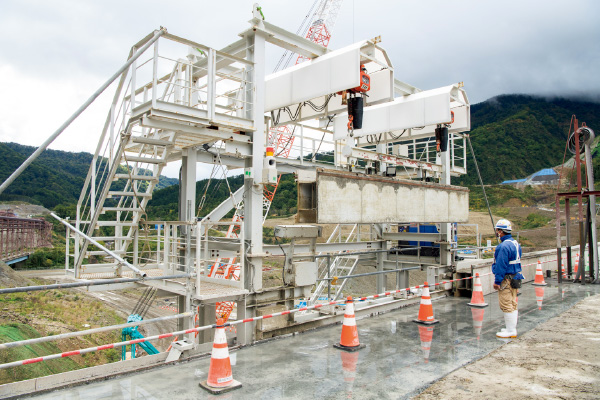
置き型枠自動スライドリフタ
photo: takuya omura
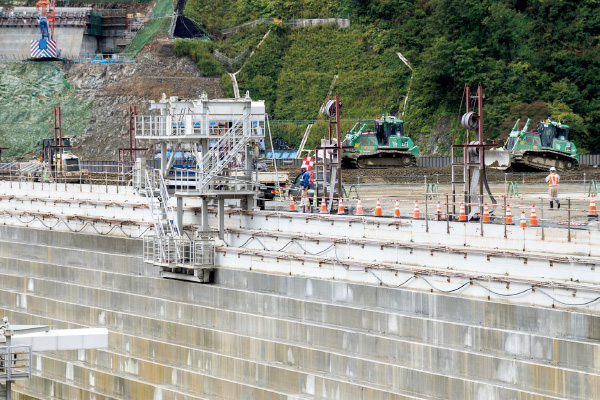
型枠の移動作業と並行して,堤体ではA4CSELが稼働する
photo: takuya omura
「A4CSEL の施工エリアから有人作業を完全に排除できれば,今以上に高速施工や省力化,コスト縮減が可能なので,課題として取り組んでいきたいと思っています。また,A4CSELを活かすためには,自動化機械に合った施工手順や方法をつくりこむことが重要なので,施工要領,作業標準,設計の見直しも必要です。これは官民を挙げて検討していく必要があります。『従来のやり方を一から見直す』という視点が重要だと思います」。成瀬ダムで深化し続けるA4CSELの今後の展開を見据え,奈須野所長はそう遠くはない未来の建設工事のあり方をこのように思い描いている。
土木の未来を体感できる
「KAJIMA DX LABO」
成瀬ダムの右岸側サイトに設置されている土木の未来体験館「KAJIMA DX LABO」は,当社が考える“土木の未来”やA4CSELの概要,成瀬ダム工事について,AR(拡張現実)を通してダイナミックに体験・学習できる施設だ。
LABOはジオラマを中心に据えたパネルゾーンとシアタールーム,展望デッキのフィールドミュージアムで構成されている。中心にあるジオラマでは,タブレット端末をかざすと,完成後の成瀬ダムが出現。成瀬ダムの役割などをARで体感し学ぶことができる。目を凝らすと現場周辺に生息する可愛い動物も隠れている。また,パネルゾーンでは,ダンプトラックとブルドーザが施工する無人の自動化施工エリアに入り込んだかのような迫力のあるARを味わえ,展望デッキでは実際の位置に完成形のダムを視認することができる。
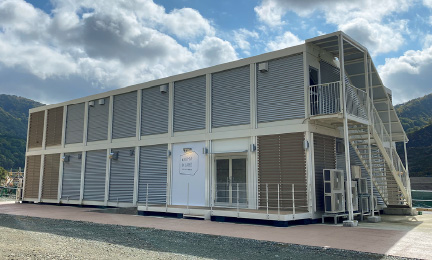
KAJIMA DX LABO外観
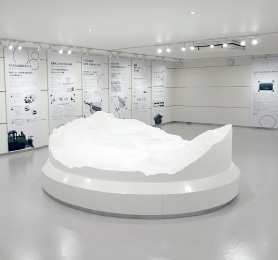
LABO内の様子。ジオラマとパネル
昨年11月には冬季休館中でも,LABOを体感できるオンラインミュージアムを開設。言語は日・英が選択でき現地さながらの臨場感でARを体験できるほか,シアタールームで上映されている動画も視聴が可能だ。
現場の見える化を支援する
ハンディ型モニター
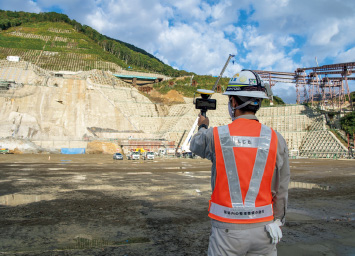
photo: takuya omura
ハンディ型モニターはAR対応のスマートフォンの画面上にCIMモデルを現場の画像に重ねあわせて表示できるシステム。
下の3枚の画像は,ハンディ型モニターを使って堤体上からダムの右岸側を映し出したAR画像。CIMモデルの透過率を任意で設定することで,上から2段目の画像のように,現在の現場の状況と計画中の仮設物や監査廊の位置関係や,工事の進捗を把握することができる。
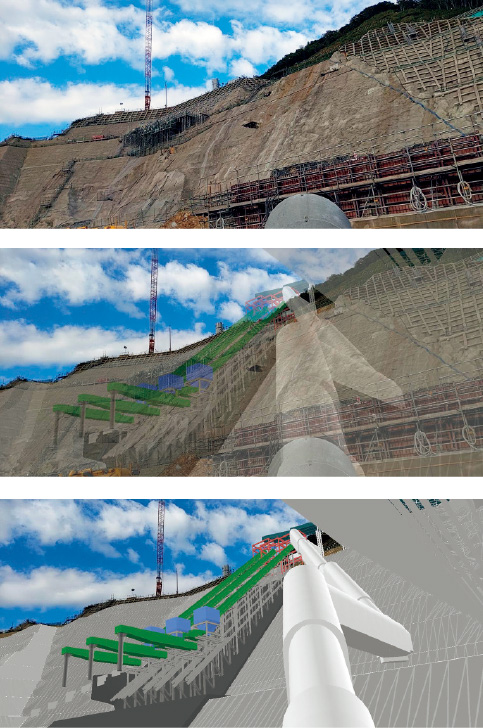