「鹿島スマート生産ビジョン」のパイロット現場に選定された鹿島伏見ビル。前ページで取り上げた18の各種技術・システムの集中的な適用・実証が行われてきた。ここではそのなかのロボット化技術を中心に紹介する。
(仮称)鹿島伏見ビル新築工事
- [工事概要]
-
- 場所:
- 名古屋市中区
- 発注者:
- 鹿島建設
- 設計:
- 当社中部支店建築設計部
- 用途:
- 事務所,店舗,駐車場
- 規模:
- S・CFT造 13F 延べ16,891m2
- 工期:
- 2018年3月〜2019年9月(予定)
(中部支店施工)
伏見のメインストリート,
錦通に面する鹿島伏見ビル
スマート工事事務所から遠隔で確認
名古屋のオフィス街に位置する鹿島伏見ビルは,1階に店舗を併設,立体駐車場を備えた地上13階建てのオフィスビル。
現場から20mほど離れたところに設けられた「スマート工事事務所」では,前面の大型モニターが「現場内モニタリングシステム」となっていて,入退場情報など現場管理に必要な情報がすべて映し出されている。現場各所に配置されたモニタリングカメラや取り付けた発信機(ビーコン)による資機材位置など,遠隔で情報を確認。また,現場内に設置されたモニターも使い,管理者は毎日の朝礼・昼礼,立入り禁止場所や施工状況などの情報を事務所にいながら共有することができる。
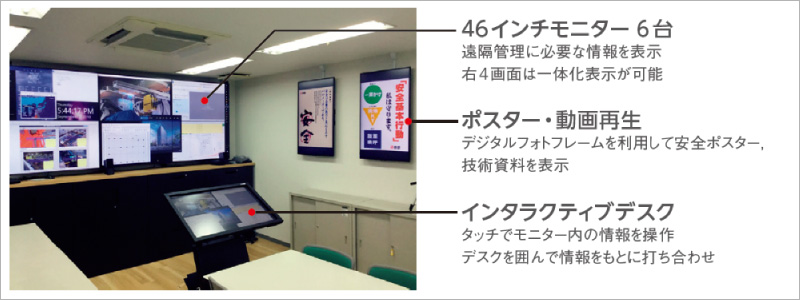
スマート工事事務所(現場事務所内に併設)は,報道陣への説明会や見学会にも使用された
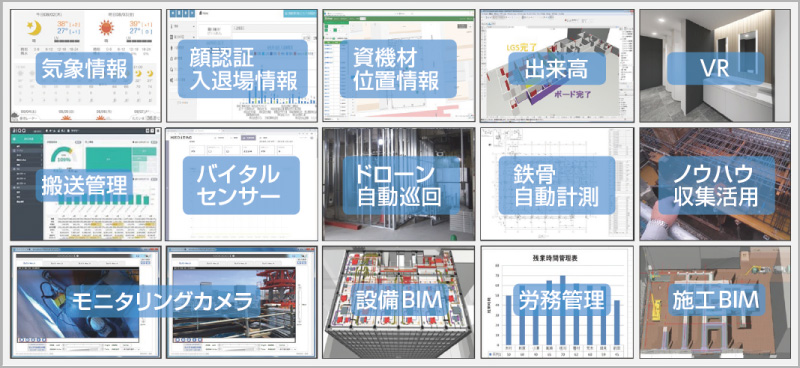
モニター表示項目例
本格導入された鉄骨溶接ロボット
今回,当ビルで実証したロボット化技術のひとつである「鉄骨溶接ロボット」。形状・肉厚の大きい柱の横向き溶接や,梁下フランジ(鉄骨部材の下側)の上向き溶接は高度な技術を要する。そこで,コア部の柱・柱接合部全周溶接の一部,柱・梁仕口部の下フランジ溶接の全箇所を溶接ロボットで施工した。あらかじめ入力されたデータとセンサによって,自動で位置や電流を調節。ロボット10台とオペレータ8名により,柱10ヵ所,梁585ヵ所の溶接作業を安全・高品質に完了した。
また,これまでロボットではできなかった角柱の四隅アール(曲線)部の溶接も行った。ロボット2台で同時に2ヵ所の対角を溶接,付け替えてさらに2ヵ所の対角を溶接した後,上側と下側の柱を仮固定していた部品(エレクションピース)を外して直線部を溶接する。現在,柱の全周を付け替えることなく溶接できるロボットの開発も進められている。
ロボットでの溶接のうち,今回とくに評価されたのは,人では技術的に困難だった下方からの上向き溶接が可能になったことだ。これまで下フランジを上方から溶接していたため上階の床を後施工していたが,その必要がなくなり,品質・安全の向上に加え,工程の短縮にもつながる。
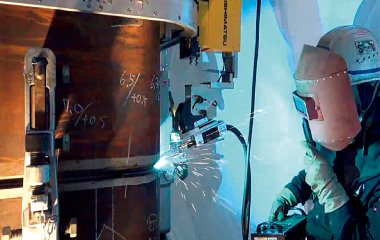
鉄骨溶接ロボットによる角柱の四隅アール部の溶接
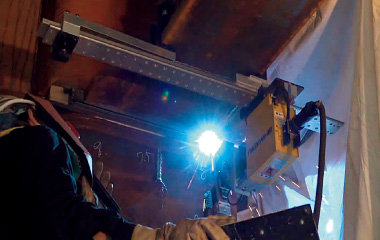
下フランジの上向き溶接の実証
ロボットによる作業負担の軽減
鉄骨の耐火被覆工事では「耐火被覆吹付ロボット」の実証が行われた。入力データをもとに,多関節型アームが耐火被覆材の自動吹付けを行う。
一般の吹付作業では,呼吸保護具や保護衣を着用するが,とくに夏の暑いときなどの厳しい環境下では熱中症の危険も伴うなど作業員に大きな負担がかかる。ロボット化によりそのような負担を軽減し,安全性・生産性の向上が図られる。
さらに,吹付けと巻付けの2通りの工法を併用する「ハイブリッド耐火被覆工法」では,吹付け後の鏝(こて)押えが不要となる。当現場では,この工法と吹付ロボットとの組合せで実証が進められた。
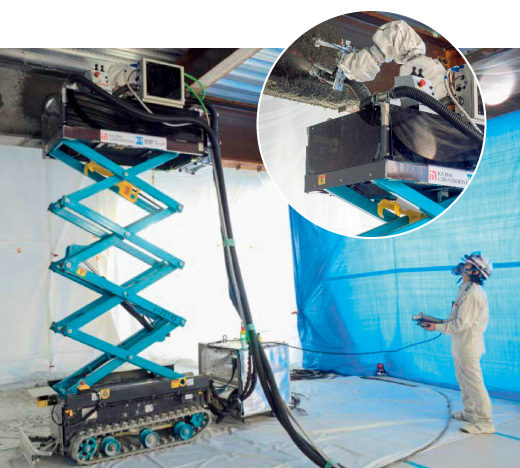
耐火被覆吹付ロボット実証の様子。ロボットの活用で,吹付けに伴う高所作業が低減する
ハイブリッド耐火被覆工法の特長
施工難度の高い梁の下フランジを作業員による巻付け,ウェブと上フランジをロボットによる吹付けとすることで,作業分担が可能となる。
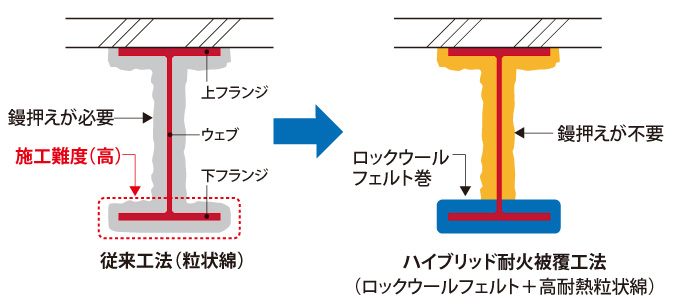
※ハイブリッド耐火被覆工法は,2018年9月に1時間耐火,2018年11月に2時間耐火,2019年2月に3時間耐火の国土交通大臣認定を取得。
作業の半分はロボットと協働
外装の取付段階では「外装取付アシストマシン」を実証。1枚200kgもの外装材を取り付けた。外装材をアームで持ち上げ・旋回・移動・取付けという動作を操作用コントローラーで操る。これまで4人で行っていた作業を2人一組で行うことが可能となる。ただし,今回使用したロボットでは,それぞれの動作が1動作ずつしか行えないことが課題。今後,連続で同時に動作することでスピードアップを図ることが求められる。
ドローンについては,始業前点検,現場状況の確認,夜間の点検など将来行われるであろう「ドローン自動巡回」の現場実証が行われた。さらに今後の活用として,ドローンによる出来形計測とBIMを連携することによる出来形進捗状況の管理なども期待されている。
そのほか,「コンクリート押えロボット」「疲労軽減アシストスーツ」「ウエアラブルバイブレータ」などのロボット化技術,また遠隔管理技術や計画・管理技術の現場実証が行われ,将来の実用化に向けたさまざまなデータ収集が行われている。
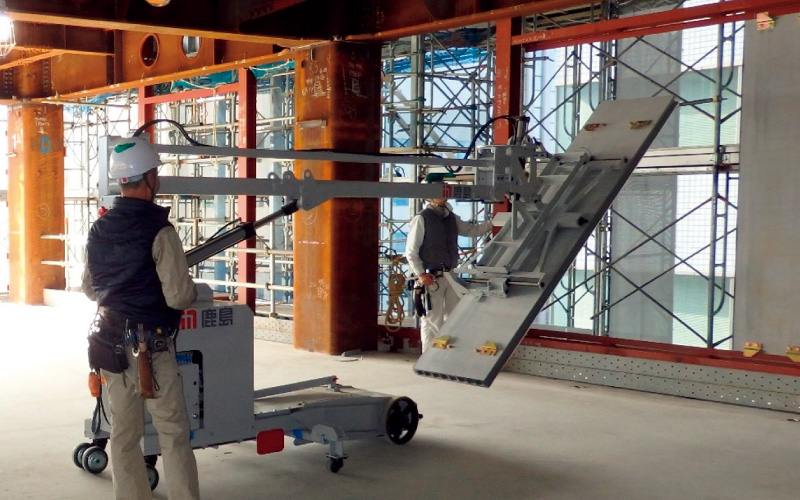
外装取付アシストマシン(マイティフェザー®)は,操縦する人と取付位置の干渉を確認する人の2人で作業を行う。今後マシンの無線化,自動化が期待される
人がつなぐ技術の革新
木村 友昭 所長
スタート当初は,正直,ロボットがどこまで人の代わりになるかは半信半疑でした。ですが,技術実証をしながら実際現場に適用してみると,これは使える技術だという確信に変わりました。明らかに作業員さんの危険や負担が軽減し,職長さんからも高評価の声を聞きました。
しかし,まだまだ改良の余地はあります。たとえば,人が行う溶接においては,作業員は風が吹いたら自分の体を風除けにするなどの細かな技を身につけています。それらを今後溶接ロボットの自動化に活かせないか,さらにほかの部分もロボットでできないかなど,現場で使ってみて気づくことが多くありました。
特殊部材の施工や複雑な調整が必要なものは人が行い,品質を確保する必要があります。人はロボットと協働し,生産性を向上させていく。これからの建築工事には,さらにロボットが進出してくるでしょう。そのためにも,現場の人にはロボットに対するアイデアや要望をどんどん出していってほしい。それが技術の革新につながっていくと考えます。
今回,同業他社のみならず,マスコミやロボット・システム関係の会社などさまざまな分野から驚くほど注目を浴びているこの現場で,多くの成果や実証データをあげることができ誇らしく思います。また,われわれ現場の人間もまさにこれからの建築の未来を感じるよい経験が得られました。