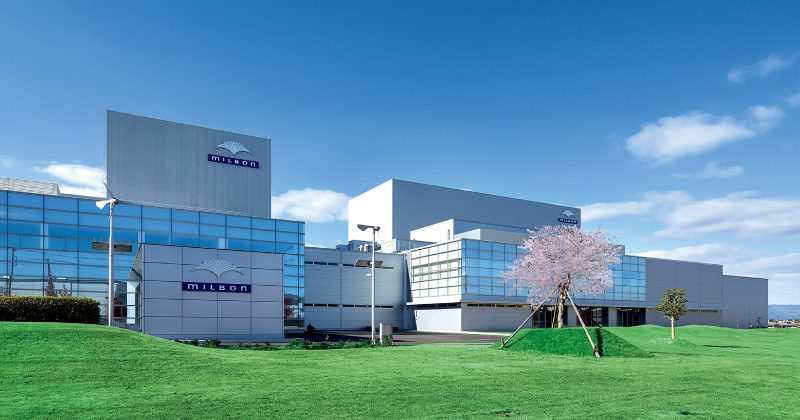
第二工場(建物右)は,第一工場(左)と共通機能をもつ建屋を中心に接続されている
ミルボン ゆめが丘工場 北棟(第二工場)
- 場所:
- 三重県伊賀市
- 発注者:
- ミルボン
- 設計:
- 当社中部支店建築設計部,
エンジニアリング事業本部 - 生産・物流設備:
- 当社エンジニアリング事業本部
- 用途:
- 化粧品製造工場
- 規模:
- S造 3F 延べ11,510m2
- 工期:
- 2015年10月~2016年12月
(中部支店施工)
既存工場と新規工場の機能統合
第一工場の竣工から9年が経過した2014年,同社は隣接敷地を取得し,第二工場建設計画コンペを実施した。ヘアカラー剤が主力だった第一工場とは異なり,第二工場ではシャンプーなどのヘアケア製品が中心となる。「多品種変量生産という,特性の異なる生産形態ですが,既存工場との機能統合によるコストメリットを打ち出すため,第一工場との接続は必須でした」(赤木次長)。
当社はエンジ本部と中部支店が一体となりプランを作成。敷地面積が広く,生産機器台数が多いため,コンセプトは第一工場と同様に自動倉庫システムを中心としたが,プランは調合室,充填包装室を人手での搬送も含めた配置とし,生産機器を柔軟に変更できるようにした。3ヵ所の渡り廊下を設置し,そのうちひとつを物流専用の動線にすることで,第一工場との有機的な連結をもたせた。こうした提案には,第一工場の計画・建設から運用支援を行った経験による,工場全体の運用方法の理解が不可欠だった。さらに既存工場のIE分析結果をふまえた運用計画を盛り込み,プランを提案。当社案が選ばれた。
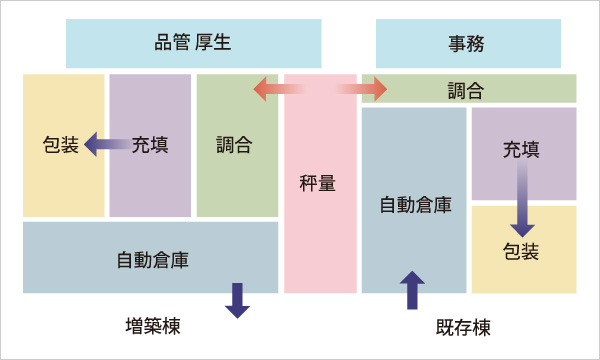
第二工場のプラン提案
生産の基本となる秤量,調合,充填,包装,自動倉庫,事務,品管厚生の各機能の関係について,既存工場を考慮して平面構成のバリエーションを検討。最終的な提案では,第一,第二工場の共通機能である入出荷,秤量を2つの建屋の中心に統合して配置し,各棟に原材料の供給および製品の回収が行えるようになっている
綿密な移転計画を策定
設計においては, 特に構造が複雑な調合室にBIMを活用し,3Dモデル上で設備の配置や使い勝手,また見学者通路から見た視線なども確認。これらのデータを協力会社と共有して,建築設備の配置計画,干渉チェック,細部の収まり検討を,早期にしかも短期間で行うことができた。
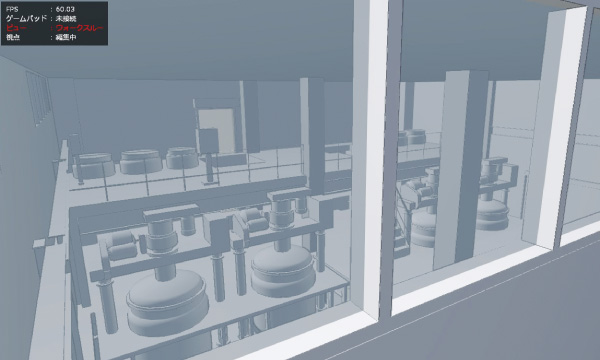
見学者通路からの視線確認(BIMモデルから作成)
移転に際しては,第一工場を止めることなく新工場を稼働させるとともに,別敷地に立つ既存工場から在庫と設備の移転を行うという計画とした。
情報システムについても,生産規模拡大に対応できる新規システムを導入。一度に切り替えるとリスクが大きくなるため,二段階での導入とした。物流設備については,第一工場の稼動状況や建設工程を調整して,新工場と接続させながら一気に入れ替えを行い,無事に完了した。
運用・保守のエンジニアリング
2016年に「ゆめが丘第二工場」が完成。エンジ本部は,稼働初期における不具合などに対応し,安定稼働が定着するまで現場に残り支援を続けた。その後も,遠隔操作におけるシステム確認や問合せに対応するなど日常的にサポートを行い,ゆめが丘工場は現在まで一度も操業を停止せずに稼働している。また生産状況の変化を見て,必要に応じ,システムの改造を別途提案することもある。運用を含めた工場全体を把握しているからこそできる提案であり,運営保守のパートナーとしての役目を担っている。
現在はIoTの活用など,さらなる生産性向上に向けた運用改善のコンセプト設計を協働で実施中だ。
未来像が組み込まれた
四次元エンジニアリング
第二工場(2016年竣工)が完成し,2工場体制となって3年が経つミルボンゆめが丘工場。第一工場(2005年竣工)から始まったゆめが丘工場のエンジニアリングの経緯を振り返りながら,当社エンジニアリング事業本部とのパートナーシップ,そして将来の展望について,ミルボン取締役兼生産本部長の村田輝夫氏に話をうかがった。

ミルボン 取締役 生産本部長 村田輝夫氏(右)と,当社エンジニアリング事業本部 赤木宏匡次長
既存工場の進化版ではない
ゼロからの発想を
業界では先駆けだった化粧品GMPへの準拠について,村田氏は「どうせなら早い段階で対応し,品質と安定化の証にして製品の価値を高めようと考えました」と語る。GMP準拠には,当時の製造施設,工程,オペレーションの全てを変える必要があった。
「GMPの規定に沿って,これまで隣同士で行っていた『秤量』と『調合』の場を別々に置き,新たに『調合室』をつくるといった製造工程が必要です。しかしそのぶん運搬の往復が生じる。そこで鹿島から提案されたのが,自動倉庫を移動兼ストックとして使う手法でした」。
当時の工場では,1階に重量のある充填機,2階を資材置き場にしていた。
「提案により,ゆめが丘工場では充填機を2階に設置しています。耐荷重の問題もあり,当時にはなかった発想です。現在は上下間の移動ができる自動倉庫を駆使し,1階に入ってきた原材料は自動倉庫に入れて,そのまま2階に移動する仕組みになっています。以前は資材の出し入れにフォークリフトを使用しており,当時の社長が最も憂慮していたリフトの危険性や,ものの置き場などの混み入った動線が,自動倉庫を中心とした流れで解消できることが分かりました。コンペは社長のひと声で鹿島案に即決でしたね」。
こうした先入観なく中身から組み立てる提案は,当社エンジニアリング担当者が足繁く現場に通って「ものの流れ」を調査し,プラン作成にあたっての問題点と解決方法を試行錯誤し検討していた背景がある。
「さまざまな視点から質問を投げ,私たちのニーズをプランにしてくれました。既に,将来の第二工場も視野に入れた提案をもらっていたほどです。まさに未来像が組み込まれた“四次元エンジニアリング”と言えます」。
施設担当者からの厚い信頼
第一工場と第二工場の竣工には約10年もの月日を挟むが,その間もエンジ本部は継続して施設運用に携わってきた。竣工後には,設備やシステムにおける使用方法のレクチャー,安定稼働の確認でしばらくの間工場に常駐。稼働後も,問題が生じた際にはすぐに連絡を取り合い,業務がスムーズに進む関係を築いている。
2014年実施の第二工場のコンペで当社案が選出された背景には,「物流の接続が大変難しいから,第一工場の運用方法を理解している鹿島に依頼したい」という施設担当者からの強い要望があった。
品質保証としての
「魅せる工場」
「第一,第二の2工場体制となって今年で3年目を迎えます。製造工場では,製造コストを下げるという目的があります。生産品目が増えた売上の追い風もありますが,この先コストを大きく下げられる見通しです。また,2014年に打ち出した10年後の売上目標を既に達成することができました。今後は,2工場体制のキャパシティのなかで,機械の高速化と労働体制の見直しを図り,稼働率を上げていく設備投資を考えています」。
当社提案の「魅せる工場」への評価の声もある。
「独立した見学者通路は,工場内に一切立ち入ることなく製造工程が見学できるようになっています。美容室やサロンの方を中心に,年間70~80回ほど見学会を開催し,製品がどのようにつくられているのか実際に見ることで,これからも安心して使用できるとか,お客様に薦められるという声,綺麗で働きやすそうな工場ですねという感想もいただきます。こうして,製造工程をオープンにして品質保証につなげています」。
今後は,スマートファクトリー化の推進に目を向ける。
「ゆめが丘工場は,自動倉庫をどう動かすかが鍵になっています。BCPに沿った地震対策や,IoTの手法を用いて生産設備の情報を吸い上げるシステム化についても相談しています」。
これまで培ってきた信頼関係をもとに,当社の総合エンジニアリング力を今後も発揮していく。
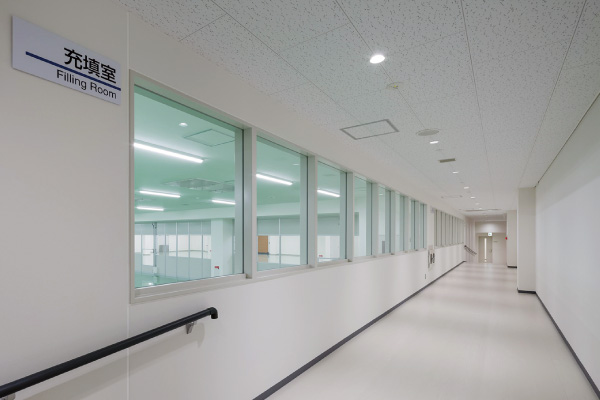
見学通路から工場内が見渡せる